Which is the Best Quality Bicycle Tools to Buy?
Which is the best quality bicycle tools to buy for a bicycle mechanic. This article helps explain the art of knowing how to invest in tools including knowing your brands, steel grades, costs and more
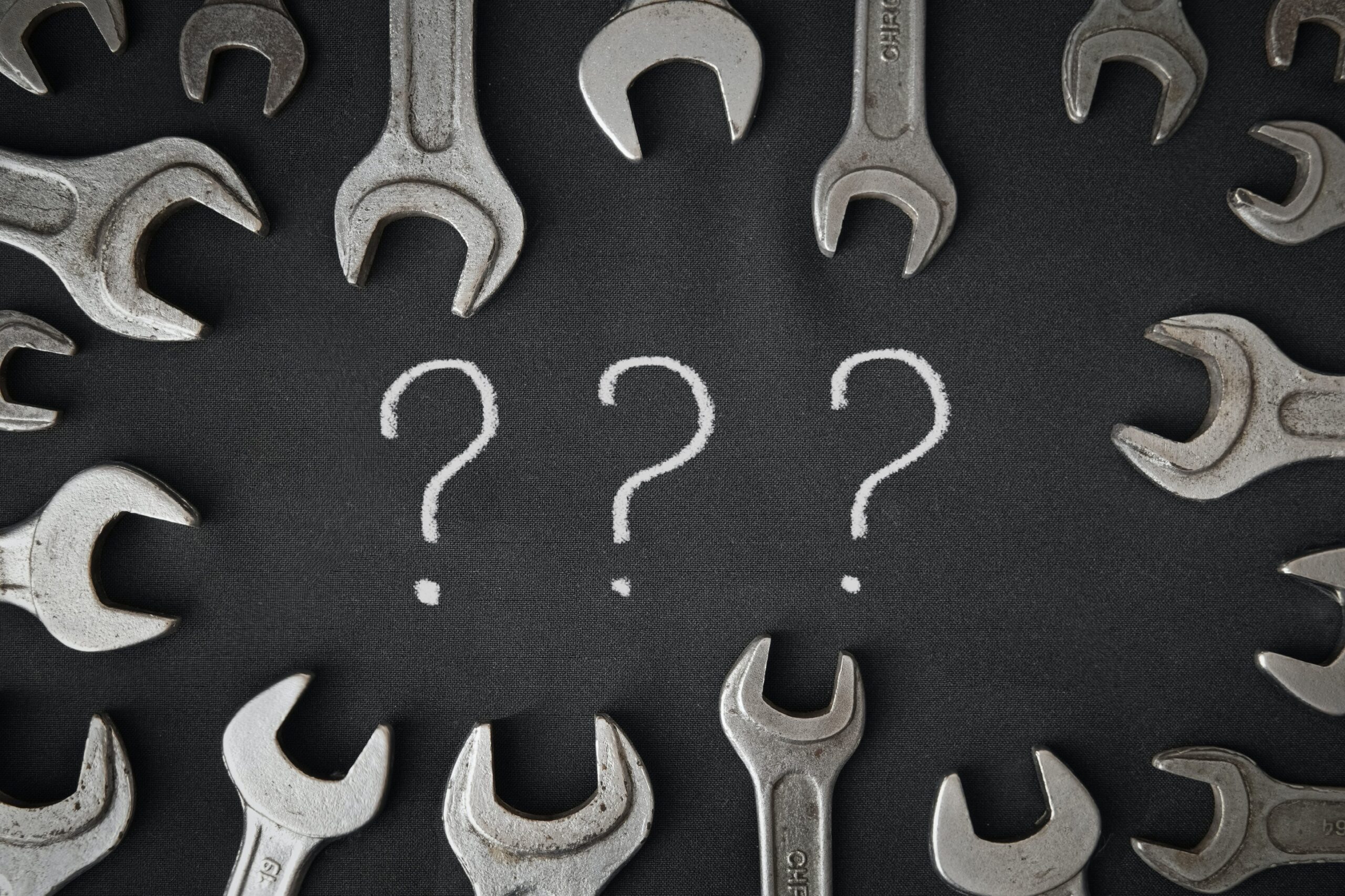
Which is the best quality bicycle tools to buy is a question I’ve often heard by many home based mechanics starting out or wanting to upgrade their tools. The answer I always give them to start with?
It depends!
People will always have a default brand they will quote as being “the best” for hand tools. You may even have heard of some common brand names and assume that they must be a good tool? but what is a good tool? What are the qualities that make a tool better than all the others?
Again, It depends!
stay with me, I’ll explain, promise!
Ok enough if that, so what do I mean by “it depends” well, it depends on the type of tool you are looking to buy, the brand, what material it is made from, quality of manufacturing process, life span of the tool, use and abuse, then the all important Price!
Truth is, I could advise specific brands and prices of tools based on my experience and I can guarantee there will be a lot of people who issue the Yorkshire battle cry of “How Much!!!!!” Who then just go and buy the cheapest version they can find because “I’m not paying that much just for a…….”
So, before going out to buy a specific tool, you need to have a clear idea in your head about exactly what you want from it otherwise you may end up spending more in the long run or worse, getting injured if it fails on you in operation. Let’s break it down into categories of what to consider when investing in a tool.
Which is The Best Tool Brand for Bicycle Tools?
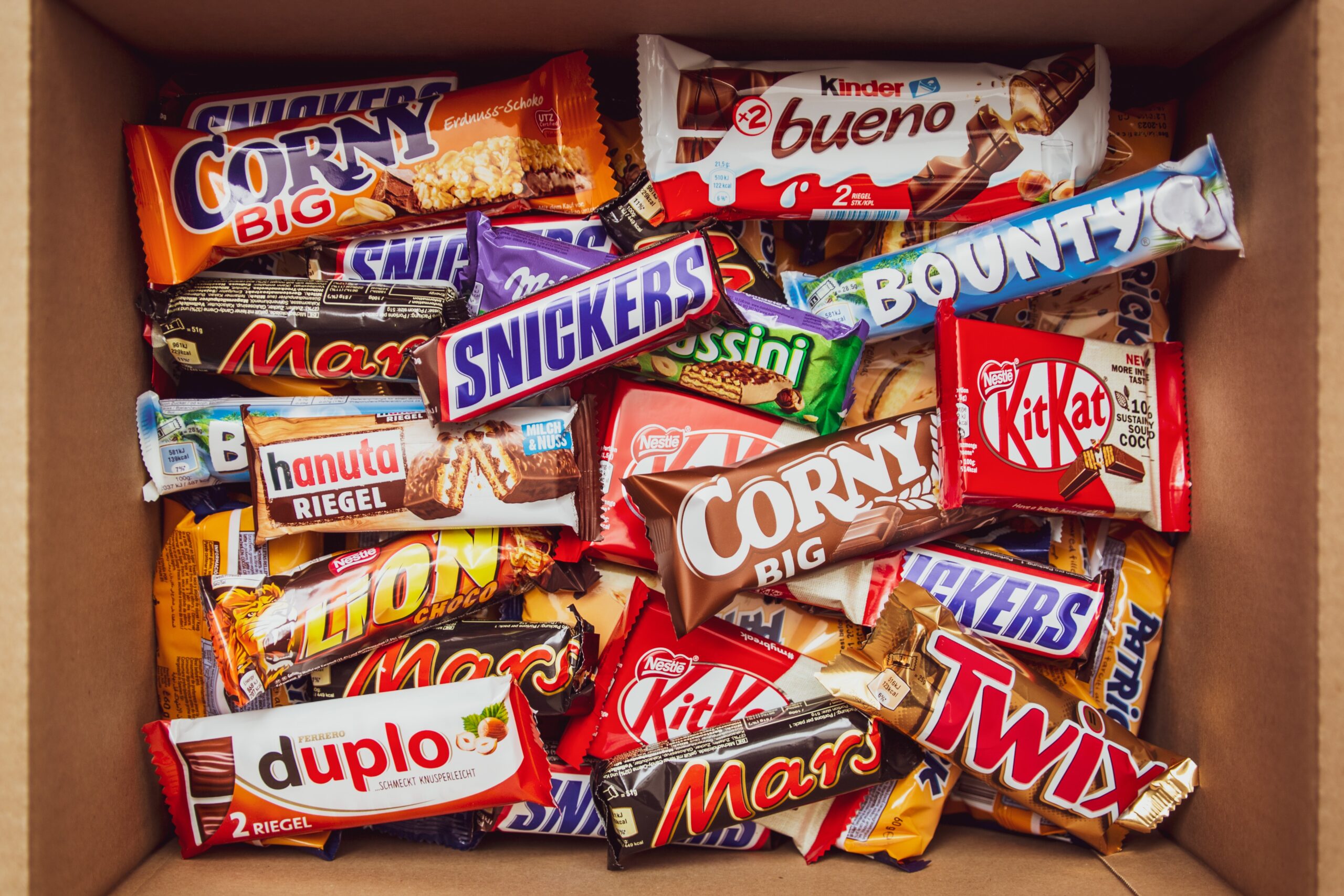
The top brand uses all the other topics together and I will discuss this one first. The Brand for tools can have a significant impact on the quality of tool you will get. Unlike in supermarkets where the difference between some value products and the premium version is all but a cost difference. In the tool manufacturer world some brands pride themselves on quality of products for professional use, whereas some focus on mass produced tools, which will likely be ok for occasional use but don’t expect them to be a significant long term investment.
Hand tools for mechanics have rarely changed in many years, as a result some tool manufacturers have been around a long time. These are the brands to watch out for as they have had many years to refine their manufacture processes to produce the best quality tools. Having said that, here’s the kicker, some of these well known brands because they have been so successful have been bought out in the past and the manufacturing moved to different countries where quality control may not be as great as it once was. Or they have shifted focus to producing mass market products rather than precision tools.
So what brands do I look for in hand tools? To help out I have put together a short list of companies I tend to look for when buying tools. The list is by no means a ranking of preference nor is it exhaustive as I am sure there are brands I have missed out that will be equally as good if not better than those listed here. This list is a guide to help you in your searches for quality tools and the brand names are links to predefined searches on Amazon.
Premium Bicycle Tool Bands
Disclosure: Some of the links below are affiliate links. This means that, at zero cost to you, I will earn an affiliate commission if you click through the link and finalize a purchase.
Channellock was founded in 1886 in Evansburg, PA by George B. DeArment. The business is still run by the DeArment family and all their products are still manufactured in Meadville PA.
Channellock was famous for its pliers, nippers and cutters. These tools still form the base of their tool production and are of outstanding quality, however they have expanded their production to include other hand tools such as adjustable wrench, screwdrivers and other specialty tools.
Bacho started out in 1862 as Högbo Stål and Jernwerks AB by Göran Fredrik Göransson in Sweden and was originally a high quality steel mill producing steel for fish hooks.
It later developed a saw blade from the steel used for fish hooks and became very successful. Later in 1892 Johan Petter Johansson invented the adjustable spanner. The company didn’t become Bacho until 1916 where it continued until 2005 when it merged with Snap-On and created SNA Europe.
Today, the tools are largely manufactured throughout Europe and not just in Sweden. They produce a wide range of good quality hand tools at reasonable prices. They may not be the best but they are worthy of being on the list.
Sealey are a relatively young company, founded in 1978 and currently operating from Bury St Edmunds UK. They have quickly established themselves as a leading tool supplier both nationally and internationally with a large range of products aimed at professionals and serious diy enthusiasts.
Their products are good quality and to demonstrate this according to their website they offer a lifetime no quibble warranty on their professional tools against manufacture defects. I can highly recommend their hand tool products, they are near the top end for pricing but they should last well if used correctly.
Klein is another US based manufacturer of quality hand tools. It was founded in 1857 by Mathias Klein and is still run by is fifth generation descendants. Klein first became famous for manufacturing quality pliers and other hand tools for the telegraph business, as the industry developed so did his business and range of tools.
Today Klein tools have a wide range of professional tools serving the electrical, construction and industrial industries. Their products are highly sought after by electrician professionals around the world and are well worth looking at for tools to use on bicycles in the workshop.
Wera was founded in 1936 in Wuppertal, Germany, making it another relatively young company compared to the others in this list. Today, they still have their headquarters in Wuppertal and also a factory in the Czech Republic.
They are well known to produce some of the finest screwdrivers for professionals, they have over 3000 products in their line now with some great looking ratchet spanners and great quality bits designed for impact drivers.
Established in 1939 by Willi Hahn in Wuppertal, Germany it was then quickly relocated in 1943 to Schonach due to WW2 where it has remained since.
They initially produced quality screwdrivers and other hand tools but in 1986 they greatly expanded their range of tools and the company also expanded with branches all over the world. They still have a strong focus on screwdrivers, bit, pliers torque tools and insulated tools amongst many others. Their products are a worthwhile investment and used by many professionals around the world.
Craftsman tools was founded in the US in 1927, they produced hand tools and electric drills. By 1932 they produced the first vanadium steel wrench, which was 50% thinner yet 200 times stronger than their previous stock.
By the 1940’s they were producing tools exclusively for aviation training schools and were considered the best tools in the US.
in 2017 they were bought by Stanley Black and Decker. Craftsman tools have a heritage for some of the highest quality tools in the US and still do today. Any Craftsman tool will likely be a smart investment.
Gedore was founded by three brothers in 1919 Karl, Otto and Willi Dowidat it was a small forge in the tool town of Remscheid. Their success saw their forge quickly grow and they moved to new premises, Stursberger Höhe in Remscheid- Lüttringhausen – still the headquarters of the company today.
They are today one of the leading premium brands in hand tools, with a product line of over 16,000 tools sold globally. The Gedore brand is split into two ranges with the Gedore range being their everyday tools and the Gedore Red for the professional market being of their best quality.
Gedore tools, especially their Gedore Red range I would consider to be in the top 3 of best quality tools.
Park Tool was founded in the 1960’s by Howard and Art. A relatively young company compared to most tool companies they formed the company from a request by Schwinn Bicycle Company for a bicycle stand Howard and Art had invented from parts laying around.
Today, Park Tool manufacture just about every tool you can think of relating to bicycles even down to screwdrivers and Allen keys. They are considered as the gold standard of tools for any bicycle maintenance professional. Owning some of their tools myself I can attest to their quality of product but don’t feel you have to exclusively own their tools there are some fantastic alternatives for the generic hand tools.
Other brands of note to be checked out are in the list below. Always research the tool spec and reviews before buying to make sure it will be suitable for your application. There are literally hundreds of brands for hand tools now from online retailers to supermarkets with some great bargains to be had.
Specialists for pliers and cutters.
Excellent range of power tools and hand tools
Professional quality power tools and a basic range of decent hand tools.
Surprisingly not bad tools given the price point, great for occasional diy use.
Which is The Best Tool Material?
Now this is where it starts getting interesting. The tool material can have a big impact on cost and performance, you need to pay attention to this detail when purchasing your tool as it’s not always well advised what tools are made from.
So, let’s have a basic metallurgy lesson to help you better understand the different common materials used to make tools. I promise not to go too technical.
Most common hand tools are made from steel. Ok, with you so far, what is steel then? Strictly speaking all ferrous steel is an alloy consisting of iron (Fe) and between 0.1 to 2.0% carbon (C). By varying the carbon content you can alter the physical properties of the steel, generally speaking low carbon content creates ductile steel (kind of like a plastic bag when you pull it it stretches before it breaks). High carbon content creates a steel which is much less ductile and more brittle, it’s not so great at resisting tension loads but it’s good in compression. Steel with only carbon as it’s alloy element is known as “plain carbon steel”
Things that are made from “alloy steels” are typically plain carbon steels with additional elements added to improve or customise the physical properties. Listed below are common alloy elements found in hand tools and why they are used.
Common Steel Elements Used in Bicycle Tools
Element | Description |
Iron (Fe) | Iron is the fourth most abundant material in the earths crust, it's the base material from which all ferrous steel is made. Iron in its pure form is so soft it can be carved with a knife. It also has a strong reaction with oxygen to create iron oxide, rust! |
Carbon (C) | Carbon is the main element to combine with iron to create ferrous steel, it formes two common compounds. Ferrite is predominantly iron with small amounts of carbon and is relatively soft. Carbides known as Cementite is the other, they are extremely hard and brittle like ceramic. By adjusting the amount of carbon you can alter the ratio of ferrite to cementite to change the hardness and ductility of the steel. |
Chromium (Cr) | This element is used in steel to increase the hardness and corrosion resistance of steel. It combines with iron and typically Nickel to create very hard stable compounds. The chromium forms an oxide layer around the compound molecule, which prevents air getting to the iron and stops rust forming. Typically used in high speed steel for cutting edges and in larger quantities to create stainless steel. |
Nickel (Ni) | Nickel is also corrosion resistant and is used along with chromium in stainless steels. Nickel also greatly increases the toughness of a metal (the ability to resist deformation) even at high temperatures and thereby increases the tensile strength. It's commonly used alloy steels and nickel based super alloys for use in jet turbine blades. |
Vanadium (V) | This element also forms carbides and nitrides in the steel mix meaning it greatly increases the tensile strength of the steel but it has the added benefit of maintaining ductility so it's easy ear to work with. It's typically alloyed with chromium to give chrome-vanadium (Cr-V) tool steel. The down side to this element is that the alloy steel can be prone to spalling on impacts. |
Molybdenum (Mo) | Molybdenum is commonly alloyed with chromium and nickel to create chromolly (Cr-Mo) steel. Molybdenum increases the toughness of a steel even at extreme temperatures. It also has good corrosion resistance and is a common element in some stainless steel grades. |
So now we know the main elements in steel, what are the main hand tool alloys and what’s special about them?
Typical Steel Alloys For Bicycle Tools
Steel Alloy | Description |
Plain Carbon Steel | This is by far the cheapest and most abundant steel. It's commonly used in budget tools and tends to have a medium carbon content so that it can be heat treated to improve its hardness and maintain toughness. Quite often they can have a chrome plating to add a level of corrosion resistance. This material while being cheap and fairly strong and hard, does not usually last as long as the alloy steels especially where high stresses occur like in wrenches. Tools made from this material are highly dependent on the quality of heat treatment to gain the best physical properties but you have to wonder, if they are using the cheapest materials are they going to be as good with quality of heat treatment? |
Chrome Vanadium (Cr-V) | Chrome Vanadium is common for hand tools and is normally used on mid to high end tools and even some budget tools are now using this grade of steel. Cr-V steel is relatively cheap compared to some other grades of steel and so it strikes a good balance between cost and good performance. The chrome gives the steal superior hardness and the vanadium along with nickel increases the strength all while maintaining a good toughness. The strength properties again are dependent on the heat treatment process, the higher end tools from quality brands tend to invest more in this process to get superior results. The down side to this material is that it can spall under impact loads, a common mistake people make is to use sockets made from this allow with an impact wrench and end up with lots of shards of metal as the socket breaks apart. |
Chrome Molybdenum (Cr-Mo) | Chromoly as this still is affectionately known as is used for its superior fracture toughness quality. It's much more expensive than Cr-V and so it tends to be only sockets and screwdriver bits that are made from this steel designed specifically for use with impact drivers. This steel uses the chrome for hardness and molybdenum to achieve greater toughness while using nickel to increase tensile strength. This steel like Cr-V uses heat treatment to get the best properties from the steel, due to it being a more expensive material it tends to be the better brands with superior quality control in their processes who use it. You can normally rely on the tools being of good quality when made from this material. |
S2 an SCVM | These are other grades of steel similar to Cr-Mo however they use different alloy elements to achieve good strength especially torsional and toughness. They are less common due to costs and availability but are equally great for use with impact drivers or tools subject to shock loading. They are normally found in screw driver bits and sockets |
Tool Manufacturing Process
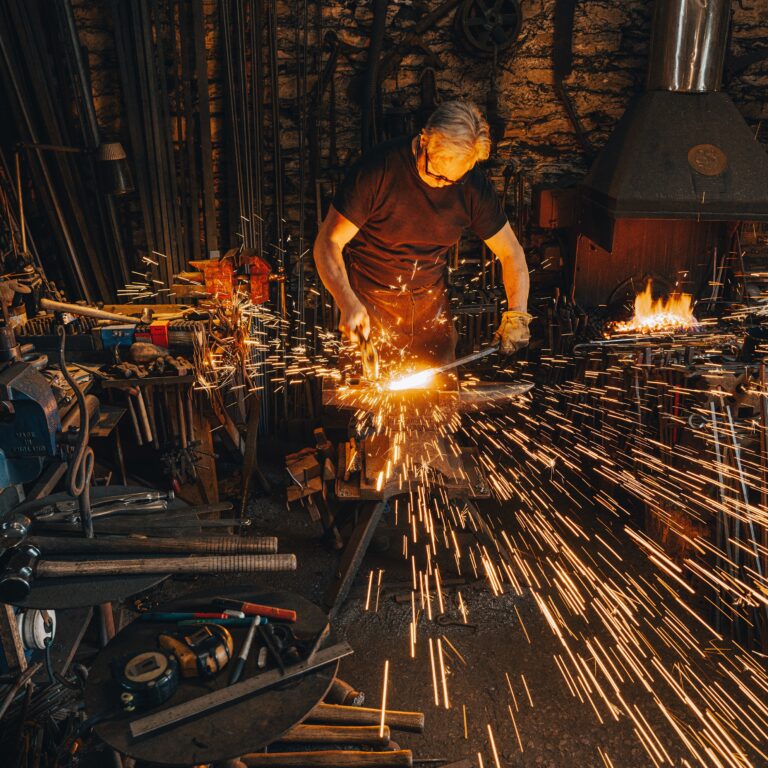
There are actually quite a number of steps in the production of hand tool and each one has a critical effect on the final tool performance. The level of investment a company makes in the production processes has a direct reflection in the quality of tool produced. I will explain the different processes in making the humble spanner, which covers most processes for hand tool.
Bicycle Hand Tool Manufacturing Process
Process | Description |
Raw Material | Chrome Vanadium (Cr-V) is usually supplied to the tool maker as flat strips of specified thickness. These strips will then be machined to form the tool blank which has a vague shape of the finished tool. Critically the tool blank will be thicker than the finished tool but not as large in plan dimension. This is the first step to a quality tool, the supplied steel should have been tested at the place it was made to verify its chemical composition. Some tool makers will perform their own tests to confirm what the steel mill certificates are saying. The difference here between budget and quality tools will be with the tool makers steel composition tollerance acceptance criteria. Lower quality steel with chemical composition that is near but not quite what it should be can be cheaper to purchase in order to produce lower priced tools. On the other hand tool makers who have strict quality control for the raw material accepted will likely charge a higher premium but have a better quality raw material to start with. |
Die Making | The next step along the journey is the production of the initial dies that are used in the forging process to form the tool blanks into the final shape under the impact and pressure of the forge hammer. Companies who make higher quality tools will spend more money to produce better quality precision machined dies with greater dimensional accuracy. The type of material used to create the dies also plays an important part of the tool geometry, the material should be using elements that produce superior strength, hardness and toughness at elevated temperatures. It should also have the least possible thermal expansion so as to maintain its shape with the high temperature blanks for forging. Correct steel for forge die making can be expensive due to the nature of the elements reared in the steel, if a company uses a cheaper alternative to keep costs down then the die can expand with the heat and become ductile under the forging blows so as to distort the final geometry of the tool and reducing the shape accuracy. |
Forging | This process is where the tool blanks are heated up to a temperature where the metal is malleable enough to be squeezed into the final shape using a top and bottom die. Normally a hammer with one half of the die attached is dropped (drop forged) onto the other stationary die with the heated metal between. Forging is in important step, it increases the strength and toughness of the steel by aligning the steel grains so that there is no open grain boundaries at positions of maximum stress in use. Grain boundaries are usually where cracks form under high stresses and can be common failure points of steel. The forging process also squeezes out minute gas bubbles and other impurities dissolved in the steel so as to minimise locations of potential intergranular crack growth. If the forging process is not properly controlled the work piece may cool to a point where it's actually becoming work hardened (deformed beyond its yield limit) this gives rise to problems with your tool breaking without applying maximum load in use. Some budget tools are not forged but instead cut from a blank piece of metal (a billet) these tools do not have the increased strength and toughness a forged item has because the steel grains have not been aligned to flow around the shape of the part. Although rare some tools are cast in moulds, these, although cheap produce inferior strength and toughness properties and should be avoided if possible. |
Trimming | Once forged, the tool will have a thin flashing around the edges where the metal flowed into the gap between the top and bottom die as they were pressed together. This flashing needs to be trimmed to give the final shape of the tool. Premium tool manufacturers will spend time and effort to fully remove this flashing and grind it smooth so that you can't tell it was ever there. This is important for two reasons; 1) so there are no sharp edges to cut hands, 2) if flashing removal is not done smoothly then the rough edges can be stress concentrations and actually weaken the tool. A premium tool will always have any flashing removed to a smooth finish. |
Heat Treament | The heat treatment process is vital to get the correct optimal hardness, strength and toughness ratios. The forging process leaves the metal in a normalised state which means it's strength and hardness is at its lowest but it's toughness is at its greatest. Tools generally need a hard surface to resist wear along with a good strength and toughness to avoid breaking when in use, but increasing the hardness of the steel generally decreases its toughness and becomes brittle. One process commonly used for tools is induction hardening, by passing a current through the tool it heats the surface up to a point where the iron carbides (cementite) dissolves into the ferrite then quenching it to lock the carbides in the ferrite to form an extremely hard surface but keeping the toughness of the main body of the tool unchanged from the forging process. This process is very cheap and normally the only process used by budget tool manufacturers, it leaves a good predictable surface hardness but does not generally increase the base strength of the tool. Premium tool manufacturers will add a full thickness quenching and tempering phase to raise the tensile strength and keep a good level of toughness before applying the induction hardening to the surface layer of the tool. |
Hardness Testing | After heat treating the tools will be tested for hardness to ensure the correct heat treatment has been achieved. For some budget brands this step may be decreased in sample number to reduce costs which means a larger percentage of tools with substandard hardness properties will slip though the net and on to the consumer. Premium tool manufacturers will likely have more strict testing procedures and higher sampling rates to ensure consistently good level of quality. |
Finishing | Finishing is the process that removes all the scale from all the heat treating and starts to make the tool shine more like it's finished state. This process is sometimes combined with the polishing stage especially with more automated processes. Some tool makers use belt sanders to do this but if not careful this can remove the surface hardness from the heat treatment. |
Polishing | After all the scale has been removed the tools are normally then polished to gain the correct surface finish. Budget tools sometimes leave this step out and instead just sand the contact areas to produce a smooth finish. Polishing is actually important for tools in high load usage, it removes any surface irregularities or rough spots where high stresses occur that could initiate a crack in the tool during use. |
Torque testing | The final factory acceptance test where the tool is tested for performance. Some premium tool manufacturers will take this stage further and subject the tool to a whole host of testing to try and determine any design flaws that may become apparent only though continued use. |
Surface Plating | The final process is the surface plating with a Chrome Nickel layer. A good, well controlled plating process can ensure a more uniform layer that will be more durable in use. Budget brands may not achieve a consistent covering and may be liable to flaking off during use leaving your tool susceptible to corrosion. |
Tool Usage and Misuse
How many times have you found yourself using a screwdriver to lever something open or using an adjustable wrench to whack something because you don’t have the correct hammer at hand?
If you are one of those people who e every tool correctly then this subject is not for you, however if you are one of those people who just grab the nearest tool you can get hold of and try making it work just because you can’t be bothered to get up and reach for the correct tool then you may need to consider this section.
Personally, I don’t condone the practice of using a tool for something it’s not designed for. If you are one of those people then you should seriously consider first using the tool properly and secondly look to well known premium brands. They are likely to have (but not guaranteed to have) designed their tools to withstand the common misuses, for example, levering the paint tin lid with a flat bladed screwdriver. Sure it may cost you more but budget brands are more likely to fail spectacularly when misused and either break ou bike or beak you.
Life Span of the Tool

Are you looking to buy a tool last you years or just wanting something cheap to do the odd job and probably never look at the tool again? This is something only you will know and will have to weigh up longevity with cost and quality before buying.
There is an old saying “buy cheap, buy twice” this is especially true with hand tools. If you are looking to invest an absolute minimum amount in a tool then it will likely be of poor quality and wear out much more quickly than you may have hoped. This may seem like common sense but sometimes we need to remind ourselves when shopping.
Personally, I like to invest more in a tool from a reputable manufacturer to last me at least a good few years, it just makes more financial sense in the long run. There are quite enough landfill issues without adding to the problem with extra packaging and broken tools. On that topic, don’t forget to recycle your discarded tools steel alloys are hhly recyclable!
How Much Should a Good Tool Cost?

Ahhh yes, now we are at the crux of the article, that all important issue of how much should you invest in a tool. Well, if yo have read all the overthrew sections to this point you will understand that as a general rule of thumb, cost is directionally proportional to the quality of tool.
Must you always pay top value for your tools though? Well, not always, what I tend to do is evaluate how hard the tool will be worked in its lifetime and how dependent am I on that tool from day to day. If the answer is that I can afford for his tool to break on me then I will use all my knowledge from above and make a significant investment. If on the other hand it’s something I will use occasionally or I know it will not see high stresses during use then I will relax a bit on price and get something that’s good enough.
When you are shopping for tools you will tend to find a million different brands if you go on any of the well known online shopping websites. It can quite often be overwhelming and very easy to buy something that looked like a bargain until you started using it and all of a sudden it starts to fail. Try using filters (price, brand, material type etc) and you will soon start to get a feel for the “right price” for the tool you need.
One last thought on price, sometimes manufactures will offer good deals on specific tools, it’s well worth watching out for these and investing even if you weren’t looking for that tool but know you will need it. Also it’s worth considering some brands you may not have thought about, for example, Amazons own brands are fairly reasonable quality, just make sure they tick all the boxes in the specification text before you buy.
How Do I Look For The Best Bicycle Tools?
- Look for hand tools that are made from chrome vanadium (Cr-V) steel as a minimum but not for use with impact drivers.
- Make sure the tool specification states it has been hardened as a minimum and preferably hardened with tempering.
- Hand tool made from steel alloy should be forged to ensure better fracture toughness and strength.
- Always consider reputable premium brands as you will benefit from their tight quality controls and advanced manufacturing technology
- Generally cost is directly proportional to quality (but not always)
- Look to the usage of the tool to help guide you with the price, if it’s going to be used often and have a hard life it’s worth investing a bit more money.
Check out some of the hand selected tools I recommend and use over in my affiliate link shop. I regularly change these links and add more tools as I find them so be sure to keep coming back to check for updates.
Thank you or taking the time to read this article, I hope you have enjoyed it. If you like my articles be sure to check regularly for new ones or even follow my Facebook page for notification of new material.